- Case Study -
Perfusion Production
Optimizing a Perfusion Manufacturing Process for Commercial Production
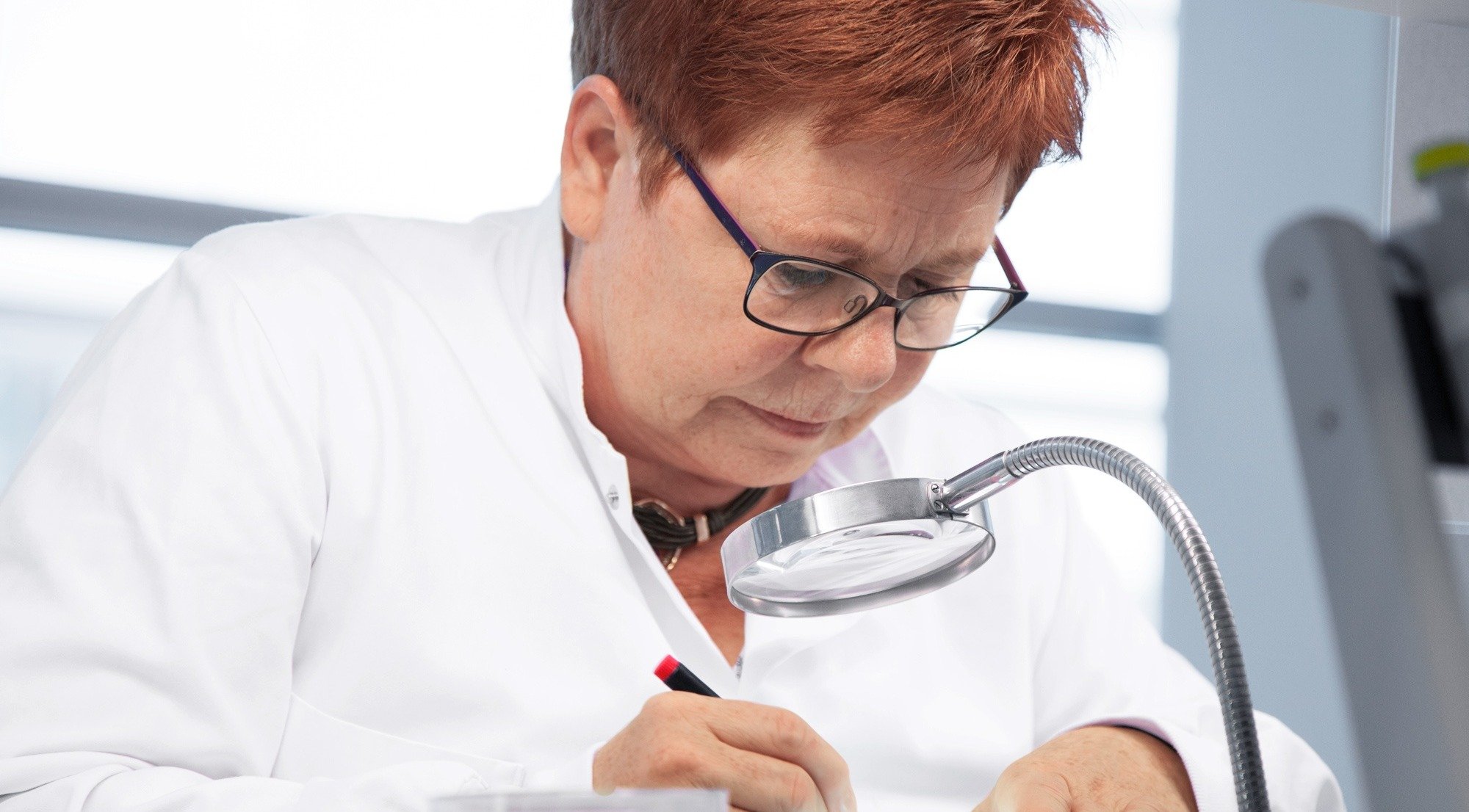
The Challenge
Optimize and scale up a bench-scale perfusion manufacturing process for a client developing its first recombinant DNA-based product. Perfusion manufacturing presents a unique set of challenges because the addition of media and harvesting of material is done on an ongoing basis, which makes it more difficult to maintain consistent conditions over the course of the manufacturing campaign. Additionally, because the material is harvested only from the media, cells need to be separated from the media at the time of harvest and then returned to the bioreactor without undergoing damage or stress that could alter protein production. The project required scale-up of a complex process and the development of validated analytics that would support commercial manufacture.
The AGC Biologics Solution
AGC Biologics was the only CMO able to meet the client’s need for perfusion manufacturing expertise. While none of the other CMOs evaluated had previous experience with perfusion, we had already conducted multiple perfusion manufacturing projects. Our perfusion-related expertise was essential for addressing the challenge associated with the technical aspects of handling the cells during the separation and harvesting phase of the production cycle.
Sonic separation methods are available but had never been used at large scale, and the existing systems were small and not sufficiently robust to support commercial-scale manufacturing.
AGC Biologics worked in close partnership with the client and with the manufacturer and inventor of a sonic separation system to optimize the technology to meet the client’s needs.
We also developed a special metric to assess the updated separation system and worked with the client and device manufacturer to upgrade the electronics in order to ensure that the device was meeting its technical requirements. We conducted multiple technical runs to demonstrate that the updated device functioned as expected, and the new metric has ensured that the system has been operating without issues for a full year. This exemplifies our commitment to doing what needs to be done to fulfill our client’s objectives.
The Client’s Success
With a robust perfusion manufacturing process in place that will support the client’s commercial needs, a conformance campaign is currently underway. The client is well on track for a successful FDA audit. AGC Biologics supports the client’s product development initiatives for manufacturing, and the client is positioned to achieve its manufacturing objectives for this product at a very high level of quality in a time- and cost-effective manner.