2 min read
MAb-solutely! New Alternative to Costly Resin Helps Antibodies Reach Clinical Milestones
Nick McDonald February 21, 2024 at 8:07 AM
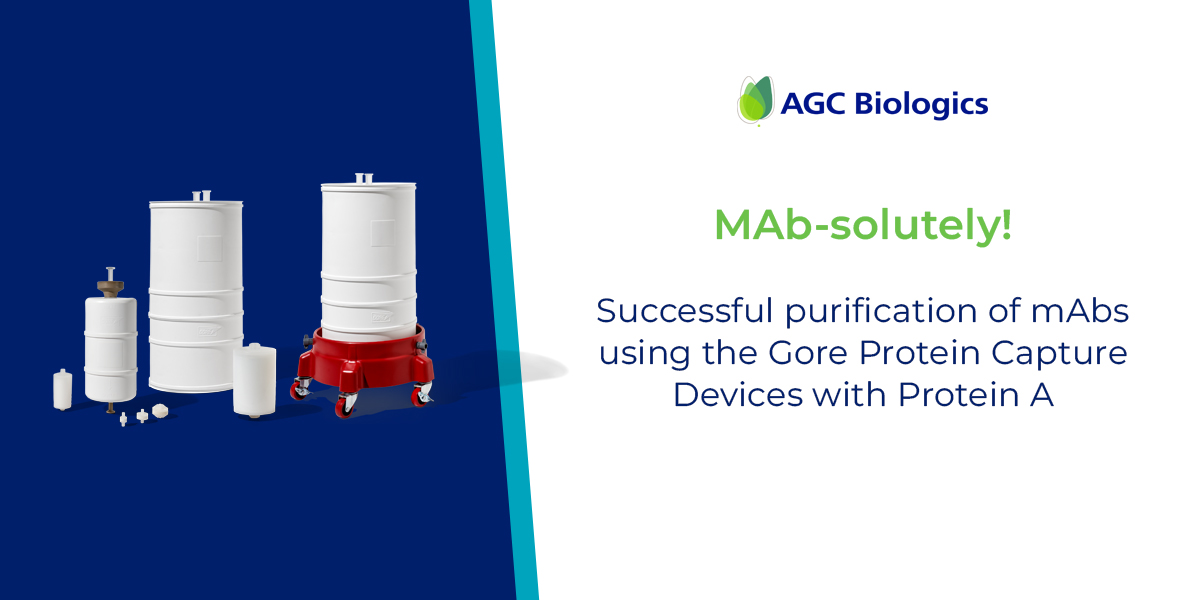
AGC Biologics’ recent white paper in collaboration with GORE discusses the development and demonstration of a high-productivity, fully single-use downstream processing platform for monoclonal antibody (mAb) production at an industrial scale. The study focuses on the use of parallel manifolded, commercially available Gore 1 Liter Devices to culture approximately 500 L of antibody harvest and purify it, demonstrating the feasibility of a full 2000 L batch.
The white paper details the experimental setup, including the process flow, upstream and downstream operations, and the results obtained from the study. It highlights the successful purification of the mAb using the Gore Protein Capture Devices with Protein A, demonstrating high productivity and critical quality attributes. The findings indicate that the fully disposable upstream and downstream platform process in antibody production is effective, as it improves production speed and productivity while reducing risk in biologics manufacturing.
What does this mean for the industry? Standard resin columns aren’t the only answer
The practical implications for the industry of using a fully single-use downstream processing platform for mAb production at an industrial scale are significant, especially for early clinical supply campaigns. The study demonstrates several key areas of note:
Improved Production Speed and Faster Paths to the Clinic: The study shows that the fully single-use downstream processing platform enables improved production speed, allowing for rapid purification of the mAb from culture harvest fluid. The process time for multiple cycles is significantly reduced, leading to faster production turnaround times. In combination with a single-use chromatography system, these devices can complete the entire protein A operation within one day (~ 8 hours) - significantly faster than resin column steps.
Risk Mitigation: The use of fully disposable upstream and downstream components reduces the risk associated with traditional biologics manufacturing processes. It eliminates column packing/unpacking, validation testing, and chemical consumption, thereby reducing contamination risk in the production suite.
Higher Productivity: The use of the Gore Protein Capture Devices with Protein A demonstrates an order-of-magnitude increase in productivity compared to traditional resin-based columns. This higher productivity can lead to increased production efficiency and throughput.
Reduced Operational Complexity: By eliminating the need for column packing/unpacking, cleaning, and storing columns and resins, the fully single-use downstream processing platform simplifies operational complexity, reducing the time and resources invested in these activities.
Scalability: The findings are extendable to multiple scenarios, enabling the purification of harvest volumes of 2000L at titers ranging up to 10 g/L. This scalability allows for flexibility in manufacturing batch sizes and supports the production of a wide range of molecules.
How does this affect CDMO Selection?
This information is crucial for CDMOs and their developer partners. The new research provides insights into a new, effective technology bringing innovation to the important downstream purification step.
Pharmaceutical developers looking to save time, money, and accelerate their timelines can adopt this new technology, currently available at all AGC Biologics global sites, to find a more efficient way to produce the antibody substance they need for early phase clinical milestones. Another important factor to consider is what type of experience the CDMO has. AGC Biologics specializes in taking your product from research and development to small scale, and ultimately to GMP scales that support late stage and commercial projects. They have successfully produced five commercial products using their proprietary cell line, guiding them through the entire clinical process.
By implementing these practices, AGC Biologics can ensure regulatory compliance, maintain high product quality, achieve operational efficiency, satisfy customers, drive innovation, and effectively manage costs. These priorities are essential for CDMOs to thrive in the competitive biopharmaceutical manufacturing landscape.
